Laser Scanning & Modeling in Mining & Tunnel Construction
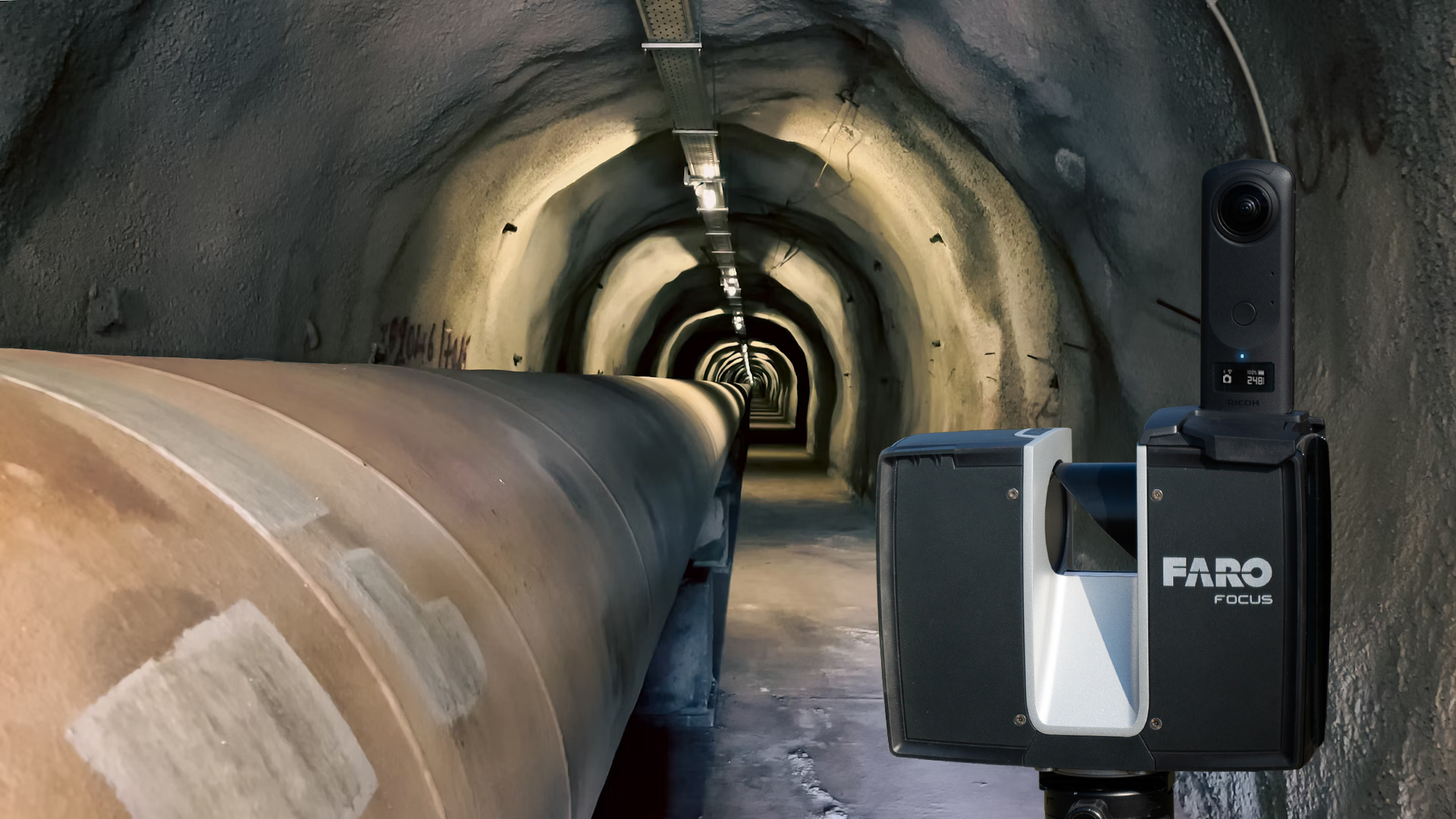
TitleDigitalization in mining & tunnelling - fast & precise
Precision and safety are essential in mining and tunnel construction. With modern technologies such as laser scanning, underground structures can be precisely measured and digitally documented.
The detailed point clouds and digital models provide an optimal basis for construction planning, geometry analysis and as-built monitoring. This saves time, costs and increases safety. Find out how digital solutions can make your projects more efficient and future-proof.
TitleSurveying in mining and tunnelling
Due to difficult conditions such as visibility, weather, geology or operational activities, surveying in mining and tunnel construction requires very special solutions in order to reduce effort, costs and time. The accuracy of penetrations and machine control place high demands on the surveying work.
One surveying method that is becoming established in this area of application is laser scanning, which masters all the requirements for such special conditions.
TitleHow are laser scanners used in mining & tunnel construction?
Exploration and mapping of deposits:
- Creation of high-precision 3D models of deposits
- Support with the planning of wind-down processes
Tunnel and gallery surveying:
- Measurement of geometries for planning and monitoring
- Inspection of tunnel linings and safety measures
Security monitoring:
- Detection of settlements and displacements in real time
- Evaluation of the stability of supporting structures
- Planning and monitoring of blasting work
Optimisation of degradation processes:
- Real-time data for monitoring mining performance
- Precise planning and reduction of material losses
TitleWhat are the advantages of digitalization in mining?
Increased safety:
- Staff does not have to enter dangerous zones
- Preventive measures through early detection of risks
- Documentation of changes in condition & visualization of earth movements with repeated 3D images possible
- Quality control and comparison with target models
Time & cost efficiency:
- Fast data capture saves time compared to traditional surveying methods
- No interruption to production required thanks to non-contact surveying
- Reduced costs thanks to more precise planning and less material wastage
- Faster building inspections thanks to precise data acquisition
Greater accuracy:
- Detailed 3D documentation enables better analysis
- Complete capture of complex geometries
- Three-dimensional capture of even inaccessible areas
Sustainability:
- Minimization of environmental impact through targeted planning and reduction of waste
TitleLaser scanning on stockpiles: Precise surveying and efficient management
Laser scanning is suitable for both surface and underground mining. Terrestrial or airborne laser scanning is used to create a three-dimensional image of terrain, structures and technical facilities. These two laser scanning methods can be used to create elevation models and calculate the volume of mining areas. Terrestrial laser scanning can also be used to record operating facilities and monitor movement processes.
Laser scanning provides accurate and reliable as-built plans and enables precise volume and mass calculations. The 3D model provides a complete documentation of all surfaces and the development. Complex cavities, such as excavation chambers or shafts, can be measured quickly and easily, construction work can be monitored and bottleneck analyses can be carried out. Even concrete thicknesses can be determined.
Measuring stockpiles is a major challenge in mining and materials management. Uneven surfaces, changing angles of repose and areas that are difficult to access make conventional methods time-consuming and often inaccurate. Laser scanners offer an efficient solution here by capturing large areas quickly and precisely and creating digital 3D models.
With laser scanning on stockpiles, operational processes in mining can be made significantly more efficient and safer. The data obtained provides valuable insights for optimal planning and resource management.
Areas of application
Volume calculation: Exact determination of the material volume, e.g. for stockpiles and invoicing
Stockpile protection: Monitoring of tipping angles and stability to prevent landslides
Inventory management: Documentation and analysis of material movements on stockpiles
Terrain modelling: Creation of detailed topographical models to optimize storage and transport processes
Advantages of laser scanning on stockpiles
Highest surveying accuracy: Precise point clouds capture even the smallest unevenness
Time efficiency: Faster data acquisition compared to manual measurement methods
Safety: Non-contact measurement without entering potentially dangerous areas
Data visualization: Creation of detailed 3D models for better analysis and presentation
Sustainability: Optimization of material usage and transport routes through accurate volume calculations
TitleTechnologies for 3D surveying above & below ground
Various scanners are used to capture data in the field of mining and tunnelling.
Mobile laser scanner
Mobile scanners, such as the FARO Orbis and the XGRIDS scanners, offer high flexibility and are ideal for dynamic environments. They can be easily transported and capture data in motion. These mobile scanners are ideal for a fast workflow.
Terrestrial laser scanner
Terrestrial scanners are static devices that impress with their high precision.
They are set up in fixed positions and provide extremely detailed measurement data, ideal for static surveying tasks.
Terrestrial scanners are primarily used for more precise measurements.
UAV-based scanning
UAV with integrated laser scanners can be used in areas that are difficult to access. This technology makes it possible to explore dangerous or unstable zones without the need for personnel to be on site.
Lights for scanning
Dark environments often present a challenge. This is where special floodlights come into play. They significantly improve the lighting conditions and ensure that scanners deliver precise data even under extreme conditions.
The floodlights are particularly suitable for use in mines and tunnels.
TitleScanning process in mining & tunnel construction
Planning
The objectives include the requirements for the as-built survey, such as geometry, condition, volume calculations and changes, as well as the identification of critical areas such as hard-to-access or unstable zones. Suitable laser scanners are selected for the preparation, e.g. mobile scanners (FARO Orbis, XGRIDS), terrestrial scanners for precision and UAVs with LiDAR for inaccessible areas. In addition, the necessary equipment (tripods, 360° floodlight) is provided and a scan plan with locations, routes and reference points is created.
Data capture on site
During on-site data capture, scanners are positioned at strategic points according to the scan plan, calibrated and their resolution and range adjusted to requirements. Capture includes both terrestrial scanning to avoid blind spots and mobile scanning for fast coverage while additional environmental data such as photos, videos and site logs complement documentation and later processing.
Data processing
Data processing involves registering and cleaning the point clouds by merging individual scans with software such as FARO Scene or PointCab, removing artefacts and noise and aligning the point clouds using reference points or natural features. 3D models, for example in the form of mesh models, are then created and integrated into GIS or CAD software for further processing.
Analysis & evaluation
The analysis and evaluation includes as-built surveys by creating cross-sections, floor plans and views from the point cloud data as well as measuring geometries. In addition, comparisons are made with previous data to identify changes such as subsidence or material loss, and the results are documented in reports that show the current condition as well as potential risks and necessary measures.
Handover of the results
The data is made available by exporting the results in common formats such as DWG, PDF or LAS and transferring them to engineers, geologists or site managers for further analysis and planning, supplemented by integration into BIM or GIS platforms to support long-term monitoring and maintenance.
Monitoring & updating
Monitoring and updating include the regular repetition of scans for long-term condition monitoring and the continuous updating of the digital twin in order to document and react to changes in real time.
TitleWhat are the benefits of 3D scans in mining & tunnel construction?
The 3D images provide a meaningful comparison of the plan and the actual measured values in mining and tunnelling. Any deviations can be corrected immediately. Due to the rapid progress of construction work in tunnelling, the tunnel profile must be checked several times for deformations. Otherwise there is a possibility that high pressure will build up due to drilling and blasting.
The laser scanner's measurements are independent of ambient light. This means that objects can be captured in three dimensions even in the dark. However, a scanner light helps enormously in the scanning process for a more precise measurement and capturing of the surroundings. In addition, the surveying effort is considerably simplified and shortened. The entire construction process can be carried out more efficiently and precisely.
The precise capturing of the object and the exact mass calculations enable more accurate construction invoicing. Contract specifications can be easily checked on the basis of final documentation. In addition, all data is also available digitally at a later date.
TitlePoint cloud analysis: Data-based decisions for mining
Point cloud analysis allows large volumes of data to be analyzed efficiently. This enables detailed geometry analyses and precise monitoring of changes in shafts and pits.
A number of software solutions have become established for processing laser scan data in mining and tunnel construction. The most user-friendly software solutions in this area include Pointscene, PointCab Origins and FARO Scene.
TitlePointscene
Pointscene offers a cloud-based platform for the management and visualisation of point cloud data. It enables central storage of point cloud data, 3D models and georeferenced maps, ensuring easy organisation and access to large amounts of data. It also supports the integration of data from laser scanners and drones, which are frequently used in mountain and tunnel surveying.
Pointscene supports the combination of point cloud data with geoinformatics or building information modelling systems as well as an accurate volume calculation of scanned areas. Another advantage is that you can use Pointscene to document and visualize changes over time.
TitlePointCab Origins
PointCab Origins software is a powerful solution for processing and analyzing point cloud data and is ideal for as-built surveys in mining and tunneling.
PointCab Origins can quickly process large point cloud data, common in mining and tunneling, and convert it into easy-to-use formats. The software automatically generates floor plans, sections and views from point cloud data, which can be used directly for the documentation and planning of galleries, shafts and tunnels. PointCab Origins can perform precise volume calculations, which are essential in mining, e.g. for the evaluation of excavation material or excavation quantities.
TitleFARO Scene
The software automatically recognizes overlapping areas in different scans and aligns them precisely to each other. This is particularly useful in complex structures such as tunnels where many scans are required. FARO Scene enables the rapid generation of 2D views and cross-sections from 3D point clouds, which can be used to document tunnel geometries and gallery structures.
Precise measurements of distances, volumes, inclinations and other important parameters are possible directly in the software. An analysis of the surface geometry is possible, for example to detect subsidence, cracks or material loss.