3D Laser Scanning & Modeling of Clean Rooms
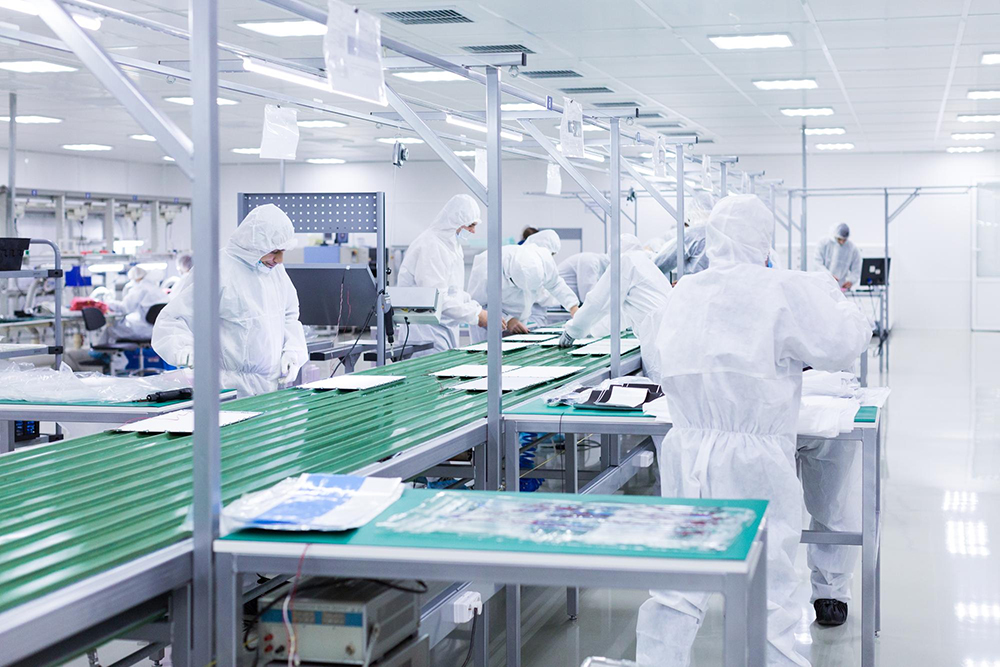
TitlePrecise planning & documentation of cleanrooms using 3D laser scanning
In sectors such as the pharmaceutical, food and semiconductor industries, cleanrooms are essential for production under controlled conditions. Precise planning and documentation of these sensitive areas is essential to ensure the highest quality standards.
3D laser scanning makes it possible to capture cleanrooms with millimeter precision and create digital twins. These digital images make it possible to plan conversions, extensions or maintenance work efficiently and without interrupting production.
Title3D surveying during the construction phase - As-built documentation
Regular as-built documentation already makes sense during the construction phase of cleanrooms. By using 3D scanners, construction processes can be continuously checked and documented, especially for projects that are carried out using BIM (Building Information Modeling). Accurate 3D documentation ensures that construction is carried out in accordance with the planning models and enables quick adjustments to be made in the event of changes.
- Checking the building shell: Early detection of deviations in construction progress.
- MEP documentation: Documentation of the technical building equipment prior to installation of the system technology.
Title3D scanning of cleanrooms after completion - The digital twin
Once the cleanroom facility has been completed, 3D scanning enables a digital twin to be created. This digital twin is an exact copy of the facility and can be used for ongoing operation or subsequent conversions without having to enter the cleanroom directly.
- Photorealistic documentation: Capture of all system components and work areas.
- Optimized process planning: Use of the digital twin for future adjustments.
TitleConversion planning with 3D scanning - Fast & precise
If a redesign or expansion of an existing cleanroom is required, 3D measurement revolutionizes the planning process. The use of 3D scanners is the quickest way to capture accurate and complete data, especially during ongoing operations.
- Layout changes: Quick capture of workstations or system components.
- Capture accurate to the millimetre: Provision of current as-built data for smooth redesign.
TitleApplication areas at a glance
As-built survey & documentation
Many cleanrooms have outdated or incomplete plans. 3D scans provide an exact digital image of the current condition, which can be used for conversions or maintenance measures.
Conversion & extension planning
With the help of point cloud data, new systems or machines can be integrated into existing structures with millimetre precision – without any surprises during assembly.
Validation & quality assurance
Regular scans make it possible to detect deviations at an early stage so that cleanliness requirements and process stability are guaranteed in the long term.
BIM integration & digital twins
The captured data can be integrated directly into CAD and BIM software to enable detailed planning and efficient collaboration between different trades.
Inspection of ventilation systems & media lines
Especially in the pharmaceutical and semiconductor industries, precise positioning of ventilation systems and pipelines is crucial. 3D laser scanning provides exact measurements for error-free installation.
Monitoring cleanroom classes & particle distribution
3D scanning can be used to regularly inspect cleanrooms to ensure that structural changes or new installations have no negative impact on airflow and particle-free conditions.
TitleChallenges in 3D scanning of cleanrooms
Reflections on stainless steel surfaces
Clean rooms in food, pharmaceutical and semiconductor production often consist of stainless steel components, which pose a challenge for optical measurement technology. Reflections on these surfaces can affect the measurement results. It is therefore important to choose the right measuring device that works with different wavelengths to deliver precise results.
- Avoid reflection problems: Selecting the right scanner technology.
- Optimized measurement technology: Modern scanners minimize interference from shiny surfaces.
Minimization of operational disruptions
Thanks to the use of modern 3D scanners, operations in the cleanroom can remain largely unaffected. Short measuring times enable the systems to be scanned quickly without disrupting the production process.
- Fast surveying: Reduced downtime in the production process.
- Contactless measurement: Minimal intervention in the cleanroom during measurement.
Avoiding contamination
Another critical point is the avoidance of contamination. When using external service providers, all measuring equipment should be thoroughly cleaned before entering the cleanroom. We attach great importance to cleanliness in our work and have, for example, purchased new accessories such as stands for measuring a medical production facility in order to eliminate any potential source of contamination.
- Maintain hygiene standards: Use of clean or new equipment.
- Specialized equipment: Surveying technology that meets the strict requirements of clean rooms.
TitleConclusion - 3D scanning as the key to efficiency
The 3D scanning of cleanrooms offers an effective way of designing planning, documentation and conversion processes precisely and efficiently. Thanks to state-of-the-art technologies such as the 3D scanner, planning reliability is increased, operational disruptions are minimized and contamination risks are avoided. As an experienced partner, we support you in selecting the right measurement technology and accompany you throughout your project.
Advantages at a glance
- Millimetre-precise measurement for precise planning.
- Minimal operational interruptions thanks to fast measuring times.
- High hygiene standards to avoid contamination.
- Digital twin for long-term planning and operational optimization.