3D Laser Scanning & Modeling in Chemical & Process Industries
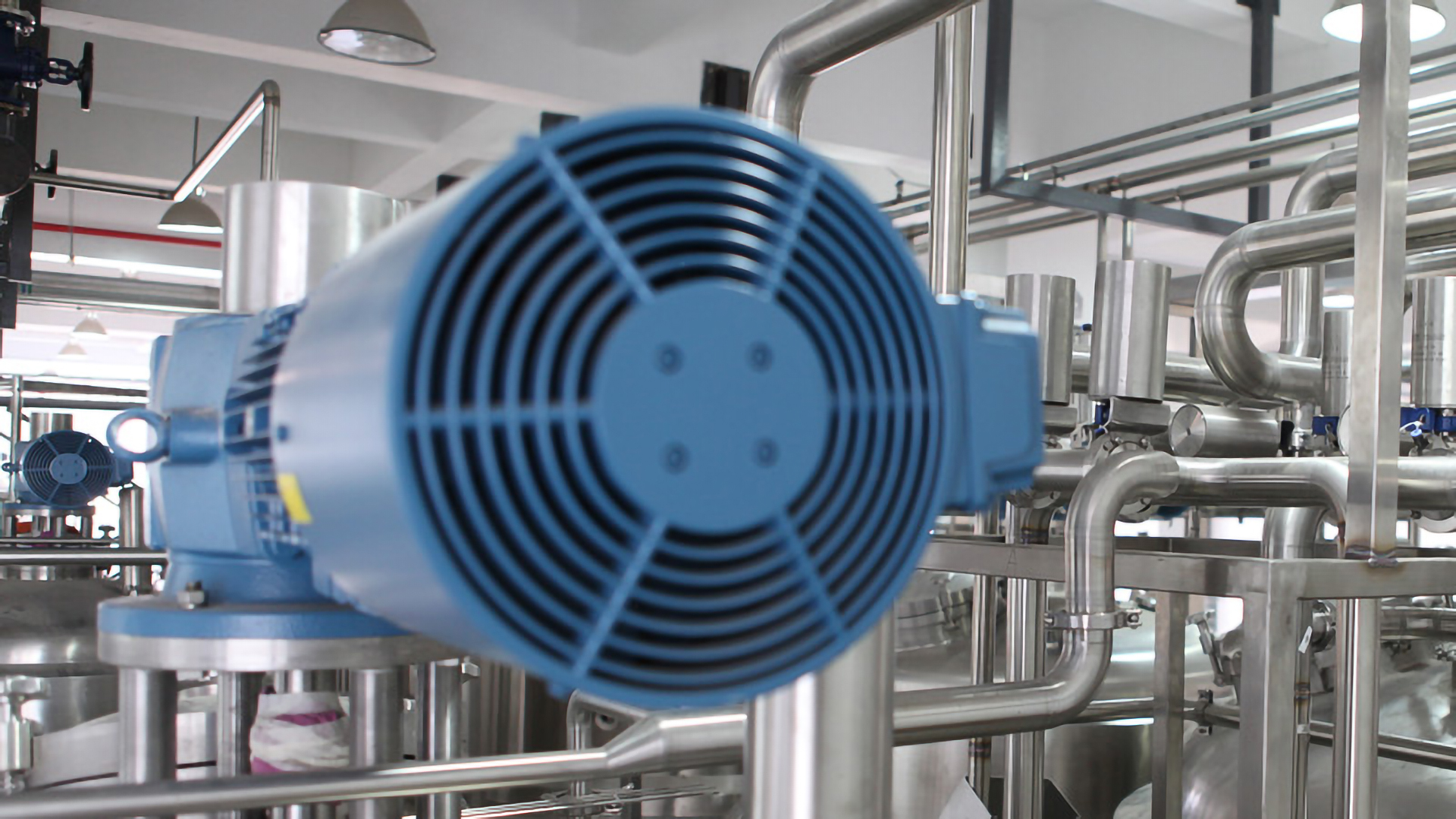
TitleDigital planning for complex systems: 3D scanning in the chemical industry
In the chemical and process industry, precise data is essential for the safe and efficient operation of plants. Complex pipelines, containers and steel structures require an exact inventory, whether for modernization, conversions or maintenance work.
3D laser scanning offers an innovative solution here: using non-contact measurement technology, even areas that are difficult to access can be precisely captured and mapped as a digital model. This creates a millimeter-precise planning basis for efficient and safe processes in chemical plants, refineries and production facilities.
TitleMissing documentation? Always up to date with 3D laser scanning!
In the chemical and process industry, many plants are inadequately documented. As-built plans often only exist in 2D or as outdated paper documents that only reflect the original design status. However, regular maintenance and conversion measures result in continuous changes that are often not updated in the plans. This results in discrepancies between the existing documents and the actual plant situation, which can lead to planning errors and inefficient processes.
3D laser scanning offers a precise, digital as-built survey that can also be carried out during ongoing operations. Even areas that are difficult to access or safety-critical can be recorded without contact – without costly downtimes or manual measurements.
TitleNon-contact surveying thanks to laser scanning
3D laser scanning captures the geometry of systems, pipelines and structures using millions of measuring points per second. A laser scanner emits laser pulses, measures the reflection and creates a high-precision point cloud – a digital image of the real environment. A highly detailed 3D model can be generated from this point cloud, which serves as the basis for conversions, extensions or predictive maintenance and ensures consistent quality assurance.
In the chemical and process industries, this technology enables non-contact, fast and reliable documentation of different areas or entire plants.
TitlePoint clouds: Valuable information at a glance
The result of laser scanning is a highly detailed point cloud that provides valuable information about the captured object. Geometries can be derived from these point clouds, in some cases automatically, and transferred to a CAD system. This enables the creation of a precise 3D model of the system, in which various views and sections can be created, resulting in
- exact as-built documentation is generated for the planning and modernization of systems.
- collision checks are carried out in the digital environment and planning errors are avoided.
- optimized maintenance processes by identifying problematic areas at an early stage.
- enabling quick adjustments to existing systems in order to seamlessly integrate new components.
TitleSustainable as-built documentation
Laser scanning provides you with complete and real as-built documentation of your facility, which accurately reflects the current condition of a facility. These precise as-built plans are an indispensable basis for modelling and modernizing your infrastructure.
The captured point clouds can be transferred to CAD or BIM models in order to detect collisions at an early stage and avoid planning errors. This ensures efficient and safe modernization of existing systems.
Thanks to the detailed plans, new system elements can be easily installed or piping adapted without the risk of collisions with existing structures.
TitleImproved quality & planning reliability thanks to digital twins
3D laser scanning provides high-precision data that takes quality assurance in the chemical and process industry to a new level. The detailed capture of the plant structure enables planning errors to be identified at an early stage and expensive reworking to be avoided.
The scanned data enables the creation of a digital twin, which serves as the basis for simulations, optimizations and long-term plant simulations.
This allows maintenance cycles to be planned more efficiently, production processes to be optimized and future expansions to be implemented more precisely – without interfering with ongoing operations.
TitleThe advantages of laser scanning at a glance
- Simple & fast: Precise data capture in the shortest possible time.
- Highly accurate & photorealistic: Detailed models of your system.
- Complete & reproducible: Every area is captured and the data can be reproduced at any time.
- Non-contact & safe: Measurements are taken during operation, even in safety-critical areas.
- Cost-saving: Minimization of downtimes and risks during planning.
- Light-independent: Works under a wide range of lighting conditions.
TitleLaser scanners in use in foundries & the steel industry
Dimensionally accurate capture of molds & casting patterns
By scanning molds and tools, deviations from the target condition can be detected at an early stage, reducing rejects and reworking.
Measurement of workpieces & components
Using high-resolution point clouds, even complex steel structures or cast parts can be precisely measured and digitally documented.
Monitoring wear & tear
Regular scans enable precise analysis of the condition of crucibles, molds or casting ladles in order to plan maintenance intervals in a targeted manner.
Optimization of production plants
The digital twin of a plant helps with the planning of modernizations and expansions without interrupting ongoing operations.
Safety & occupational safety
Critical areas such as blast furnaces or casting lines can be captured contactlessly from a safe distance, eliminating the need for manual measurements in hazardous zones.
Digital documentation & traceability
3D laser scanning enables seamless documentation of systems and components. This facilitates quality assurance, traceability and certifications in the steel industry.