3D Laser Scanning in Foundry & Steel Industry
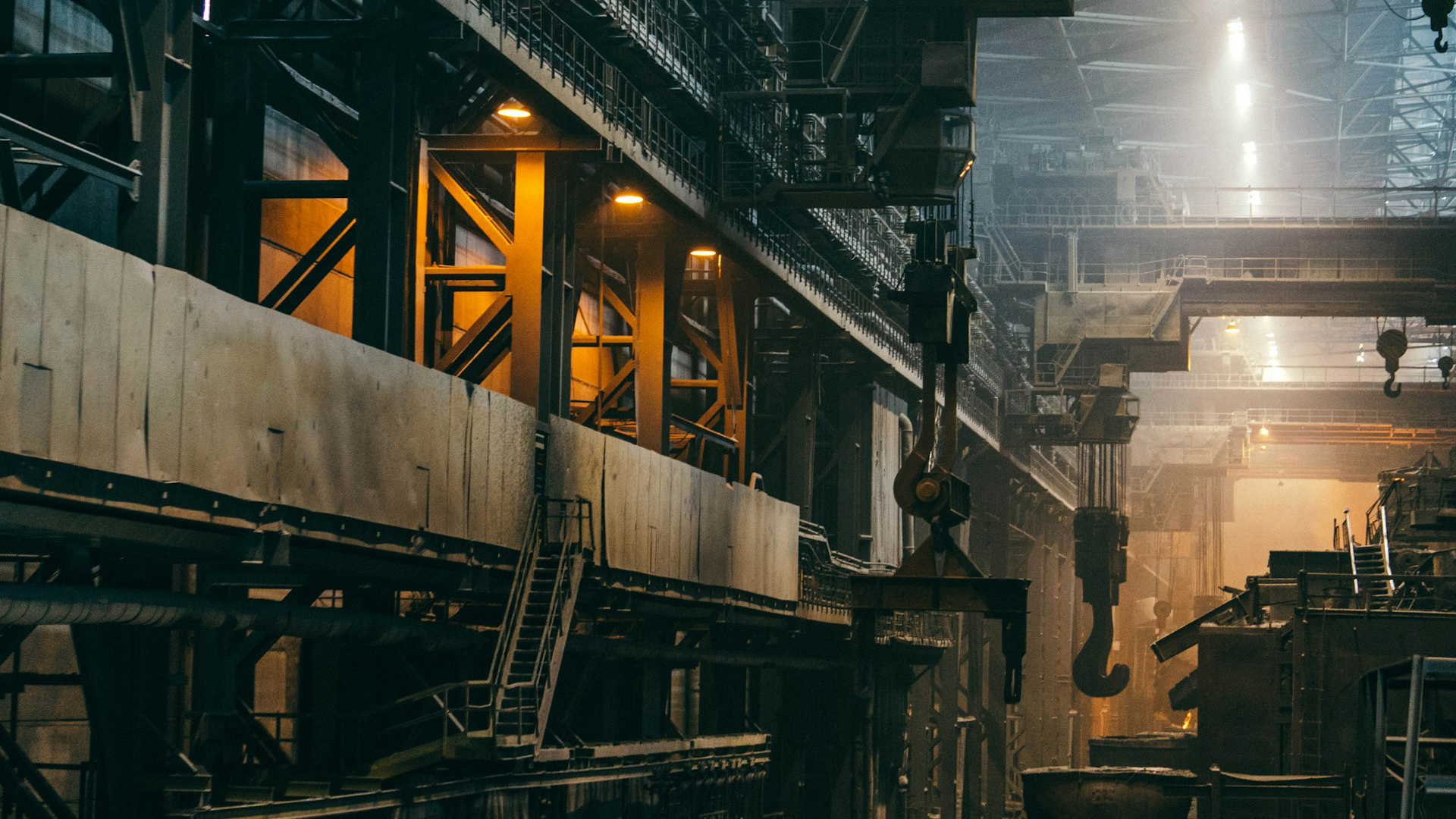
TitleModern measurement technology for foundries & steelworks
In the foundry and steel industry, precise measurement and digital planning are crucial for success. 3D laser scanning is revolutionizing this sector by enabling fast, accurate and non-contact surveying of components and surfaces.
With state-of-the-art laser scanning technology, we create the basis for efficient production processes, improved quality assurance and optimal use of resources.
TitleAreas of application for 3D scanning in foundries & the steel industry
Mold & tool measurement
3D laser scanning enables high-precision measurement of molds, dies and tools. This allows wear and deviations to be detected and corrected at an early stage, which extends the service life of the tools and reduces rejects.
Quality control & component inspection
3D scanners can be used to capture cast parts and steel components in detail in order to check dimensional accuracy and surface quality. Target/actual comparisons with CAD data make it easier to identify production deviations and improve quality assurance.
Reverse engineering for spare parts
Foundries and steelworks often require spare parts for older machines for which design drawings no longer exist. With the help of 3D scanners, existing components can be digitized and reconstructed for post-production or optimization.
Digitization of plants & production facilities
With 3D laser scanning, complete production facilities can be captured and mapped as a digital model. This data serves as the basis for conversions, expansions or modernizations without the need for physical measurements on site.
Deformation & wear analysis
Regular scans allow deformation and wear on machines or steel components to be captured. This allows maintenance measures to be planned in a targeted manner before costly breakdowns occur.
Casting & weld seam inspection
Laser scanning offers a fast and non-destructive method for inspecting weld seams and cast parts. Defects such as cracks, porosity or dimensional deviations can be detected and documented at an early stage.
Temperature-induced deformation analysis
High temperatures are a challenge in the steel industry. Repeated scans can be used to analyse thermal deformations and optimize design adjustments to ensure stability and durability.
Process optimization & automation
3D laser scanning provides high-precision data for the automation and optimization of production processes in foundries and the steel industry. By accurately capturing components, machines and conveyor systems, robot controls and CNC programs can be calibrated more precisely. This leads to more efficient production, reduces the use of materials and minimizes energy consumption.
TitleComponent surveying: Precision in every dimension
With 3D laser scanning, components are captured completely and true to scale. The data can be precisely analyzed and used to optimize production processes. Even complex components can be inspected quickly and reliably, making time-consuming and error-prone measuring methods a thing of the past. This significantly reduces the inspection times for castings.
Advantages:
- Precise measurement of workpieces and blanks
- Fast data acquisition and simple analysis
- Efficient quality control, even for complicated components
TitlePatterns, dies & molds: Precise dimensional control
Laser scanning allows models, dies and molds to be precisely measured and compared with the raw part drawings. Deviations are immediately visible, which enables quick correction and tracking. The recorded data is also available for later analysis and contributes to the continuous improvement of the production process.
Advantages:
- Direct comparison of measurement results with drawings
- Quick identification of deviations
- Reusable data for later analysis
TitleProduction plants & production lines: Increased efficiency due to precise measurement
3D laser scanning not only offers considerable advantages in the precise measurement of individual components, but also in the capture of entire production facilities and production lines. The precise and complete capture of systems, pipelines and conveyor belts creates a comprehensive 3D model that enables a detailed analysis of the infrastructure. This data can be used to plan and optimize work processes more efficiently, as possible bottlenecks or potential for improvement can be identified at an early stage. The fact that ongoing operations do not have to be interrupted is particularly valuable - even areas that are difficult to access or safety-critical can be captured without contact and without stopping operations. This allows conversions or modernizations to be planned and carried out precisely and efficiently, minimizing downtimes and increasing productivity.
TitleAdvantages of laser scanning at a glance
- Fast & efficient: Significantly reduces measurement times
- Highly accurate: Measurement results accurate to the millimeter
- Photorealistic: Complete and detailed 3D models
- Non-contact: Safe and trouble-free, even during ongoing operations
- Cost savings: Reduced downtime and faster project implementation
- Flexible to use: In complex and difficult to access areas
- Reproducible: Data available for later evaluations and planning