3D Laser Scanning for Quality Control & Inspection
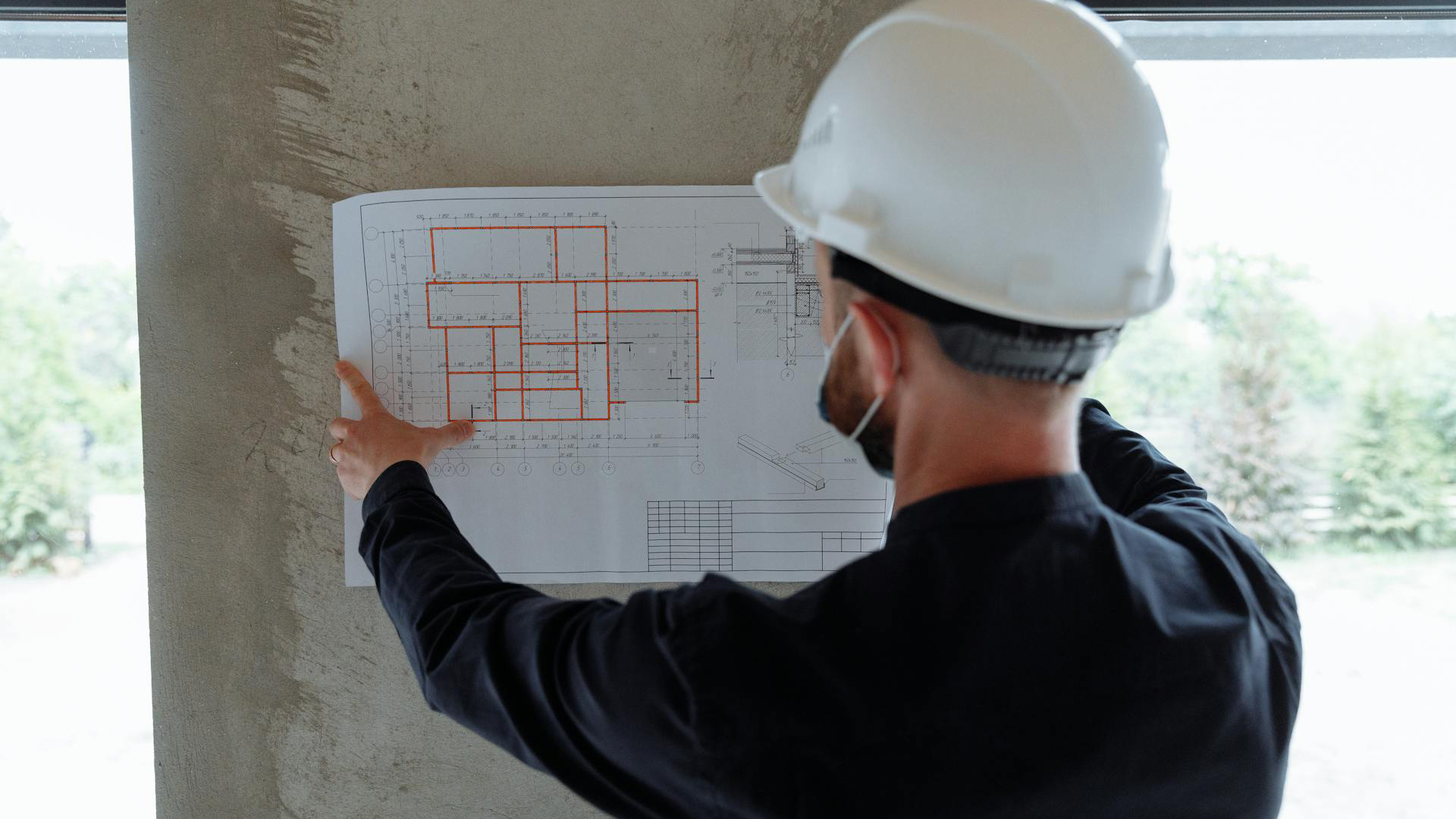
TitleOptimize your quality processes with precise 3D technology!
Maximum precision and quality assurance are crucial in modern manufacturing. 3D laser scanning offers a revolutionary way of measuring parts and components quickly, contact-free and with the highest accuracy.
Whether in the automotive industry, mechanical engineering or aerospace - laser scanning can be used to check geometries, detect deviations at an early stage and optimize manufacturing processes. This reduces error costs and raises product quality to a new level.
TitleAdvantages of 3D inspection
- Highest precision: With accuracies in the millimeter range, even the smallest deviations that are difficult to detect with traditional methods are detected.
- Time efficiency: Where manual inspections are often time-consuming and error-prone, a 3D scan delivers comprehensive results in just a few seconds.
- Automation: The fully automated comparison of the scanned point cloud with the target geometry reduces the workload and speeds up quality control.
- Cost reduction: Early detection of errors minimizes rejects and rework, resulting in significant cost savings.
TitleAreas of application for 3D laser scanning in quality control & inspection
Component measurement & dimensional accuracy testing
With 3D laser scanning, components can be precisely measured and checked for dimensional accuracy. This is essential for quality assurance in sectors such as the automotive, aerospace and mechanical engineering industries.
Series production & random sample inspection
In mass production, laser scanning ensures fast and automated spot checks. Deviations are detected at an early stage, reducing rejects and avoiding production errors.
Target/actual comparison of components
By comparing the captured 3D data with the CAD models, deviations can be identified with millimeter precision. This is crucial for compliance with strict quality standards.
Assembly check & accuracy of fit check
By capturing components and assemblies in detail, it is possible to check whether all components fit together perfectly. This prevents assembly errors and reduces the need for rework.
Surface inspection & defect analysis
Laser scanning detects even the smallest material defects, cracks or deformations on components. This enables reliable quality control before defective products are further processed or delivered.
Wear analysis & maintenance planning
3D laser scanning makes it possible to precisely capture the condition of machines, tools and components over long periods of time. Regular scans allow signs of wear to be detected at an early stage, enabling proactive maintenance planning and a longer service life for the systems.
TitleIncreased efficiency through automation
Automated inspection with 3D laser scanners is revolutionizing quality control in numerous industries. The use of high-precision laser technology not only speeds up inspection processes, but also makes them more reliable.
Advantages of automated inspection:
- Faster inspection processes with consistently high precision.
- Reduced susceptibility to errors thanks to automated data processing.
- Optimized series inspection for larger quantities, which significantly increases productivity.
- Integration into existing production lines, enabling seamless and continuous quality control.
- Seamless documentation for traceability, which makes subsequent analyses or certifications possible.
TitleThe digital inspection process
The 3D inspection process begins with a scan of the component. A laser scanner is used to capture the object from various angles to create a complete point cloud. This point cloud is then compared with the target geometry of the component. Deviations are detected automatically and can be highlighted visually.
Steps in the inspection process:
1. Scan of the component: Capture the real geometry in just a few minutes.
2. Create point cloud: Merging of the scanned data.
3. Comparison with 3D model: Comparison of the actual data with the target geometry.
4. Visualization of deviations: Colored marking of dimensional deviations.
This process can be carried out not only in the production environment, but also directly on the construction site using mobile 3D scanning technology.
TitleConclusion: Precision & efficiency in quality assurance
With the advancement of digitalization and automation in industry, the use of 3D laser scanners is not only a modern, but also an indispensable method of optimizing quality control. The technology is increasingly being used in various sectors to make processes more efficient, cost-effective and precise.
Automated inspection with 3D laser scanners has the potential to completely replace traditional methods of quality control – and thus offer a decisive competitive advantage.